Le tamahagane, l’alliage secret de l’authentique katana
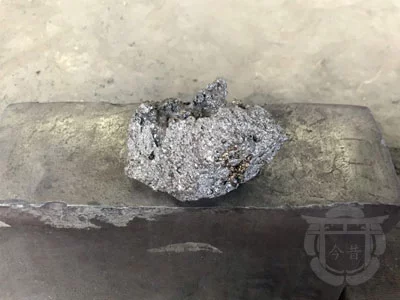
Une lame en acier forgé par les éléments
Au Japon, le forgeage de katanas respecte un code et utilise des techniques très précises qui se transmettent de siècle en siècle. Avant toute chose, il est important de comprendre que forger un sabre est pour l’artisan japonais un acte sacré, fortement lié aux forces de la nature qui seront mises en jeu pour réaliser les lames.
Par conséquent, toute la démarche sera marquée par les exigences shintoïstes :
- un autel shinto est mis en place sur le lieu de la forge ;
- les rythmes de la lune sont respectés selon les étapes ;
- etc.
Pour réaliser ses katanas, le forgeron japonais a besoin de matière première. Or le minerai de fer présent au Japon se présente le plus souvent sous forme de sable noir, dont la teneur en fer est le plus souvent inférieure à 1 %.
Transformation du fer en acier
La première étape du travail du forgeron va donc être d’extraire ce fer en « fondant » le sable ferreux pour ensuite en sortir un matériau plus noble, le tamahagane.
C’est une étape importante qui demande plusieurs jours de travail avec une température de cuisson atteinte dans les fourneaux, les « tatara », de près de 1400 degrés. Pour 8 tonnes de sable et environ 13 tonnes de charbon de bois, on arrive à extraire au mieux 500 kg d’acier propre à la fabrication des katanas.
La qualité de cet alliage est essentielle à la réalisation d’un vrai katana japonais de qualité. Sa réalisation ne dépend pas que du sable de départ, mais surtout de la qualité de l’extraction du fer de celui-ci avec un ajout d’oxygène et de carbone au bon moment et dans les bonnes proportions. La haute teneur en carbone des lames est caractéristique des sabres japonais.
Cette recette est le secret bien gardé du forgeron. On considère qu’un bon alliage doit posséder un aspect brillant argenté, une structure cristalline fine et une bonne densité.
Fabrication d’un katana : l’art du pliage de l’acier
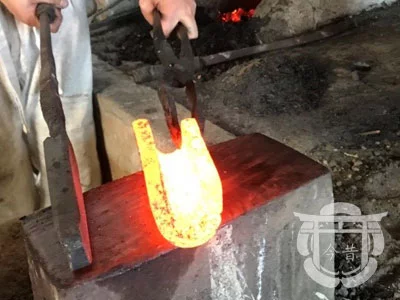
Choisir le bon alliage pour une lame équilibrée
A partir de cette matière première, le forgeron va séparer les parties « dures » et les parties « tendres » qu’il associera ensuite pour former une lame solide à la coupe inégalable.
En l’occurrence, pour réaliser des lames tranchantes, on a tout intérêt à sélectionner un acier « dur » lequel permettra d’avoir un fil de grande finesse. Mais un tel matériau est relativement fragile : un choc un peu violent et la lame casse.
La technique du forgeron japonais est donc de sélectionner dans le tamahagane un acier dur pour la partie coupante de la lame, qu’il associera avec un acier plus tendre pour apporter de la résistance.
En pliant l’acier, il obtiendra un feuilletage formé de parties dures dédiées à la coupe et de parties en acier tendre garantissant la solidité de la lame. L’aspect du feuilletage est la signature des forgerons, comme pour les lames Damas.
Séparation des aciers
Pour séparer les parties dures des parties tendres de l’alliage, le forgeron procédera au chauffage au rouge à haute température, puis à la plonge de petits morceaux extraits du bloc de départ.
Les éléments qui seront alors faciles à briser et qui présenteront un aspect grisâtre seront réservés pour le fil de la lame du fait de leur haute teneur en carbone (acier « dur »), tandis que les parties de couleur plus blanche, et donc faibles en carbone seront identifiées comme acier tendre.
L’ensemble des morceaux durs, d’une part, et tendres d’autre part sont ensuite fusionnés pour ne donner que deux briques, l’une d’acier dur et l’autre d’acier tendre.
Le fait de passer et repasser ainsi les éléments sous le marteau a un effet bénéfique pour la lame : le métal se trouve ainsi comprimé un nombre important de fois, éliminant au fur et à mesure le maximum d’impuretés.
Chacune de ces deux briques est alors pliée et repliée de nombreuses fois afin, là aussi, de persister dans la volonté de supprimer les impuretés. La tradition veut qu’on procède à 23 pliages.
Formation de la lame courbée du katana
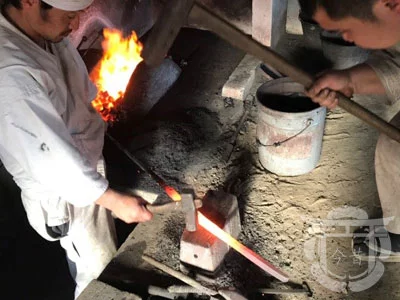
Une fois nos briques suffisamment pliées pour être débarrassées d’autant d’impuretés que possible, il s’agit de les assembler pour former la lame.
Il existe différentes formes d’association.
La plus courante nommée « honsanmai », utilisée depuis le XIIIe siècle, enrobe un cœur en acier dur avec un acier semi-tendre, tandis que le dos de la lame est formé d’acier tendre et donc solide.
Avec le temps et selon la technique employée par certains maîtres, l’assemblage a connu des variations notables. Pendant la Seconde Guerre mondiale par exemple, on réalisait la plupart des sabres suivant la méthode dite « kobuse » qui consiste à avoir un cœur d’acier doux simplement entouré d’acier dur sur les deux faces et le fil, bien entendu, le dos laissant émerger l’acier doux.
L’assemblage consiste à souder les briques suivant le modèle voulu, puis de les allonger pour former la lame suivant la courbure et la longueur voulues.
C’est cette belle lame courbée et équilibrée des sabres japonais qui fait la fierté des artisans et qui est caractéristique des sabres de samouraïs utilisés dans le Japon féodal.
Fabrication d’un katana : un tranchant à toute épreuve
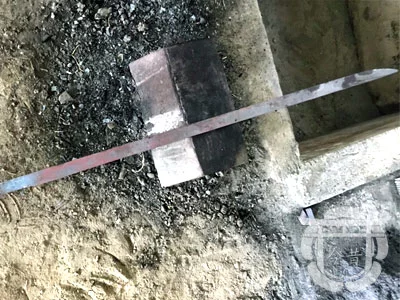
La réalisation d’un bon sabre ne dépend pas que de la qualité de la forge même si cette étape demeure essentielle. En effet, une bonne lame dépendra également de sa trempe.
Cette étape permet de réaliser le tranchant de la lame. Les forgerons japonais ont la particularité de réaliser une trempe partielle qui permet de conserver la souplesse de la lame en dehors de la partie tranchante.
La technique consiste à recouvrir une partie de la lame d’un mélange d’argile, de charbon, de bois, de silice et d’ajouts dont chaque artisan a le secret. On protège ainsi le dos et les côtés de la lame du refroidissement brutal de la trempe afin de conserver leur souplesse tandis que le tranchant, lui, gagne fortement en dureté.
Même si cette méthode de trempe fut créée à une époque où la science n’était pas assez avancée pour comprendre les effets qu’elle avait sur la structure moléculaire de l’acier, il demeure encore aujourd’hui très difficile de fabriquer un sabre de qualité comparable à celle des lames encore réalisées par les maîtres-forgerons japonais. La lame trempée japonaise est d’une dureté inégalée.
C’est ce processus qui forme le hamon (ligne de trempe). Selon son école, chaque forgeron donnera au hamon une forme particulière. En soi, la ligne du hamon est donc déjà une forme de signature.
Les étapes de finition des katanas
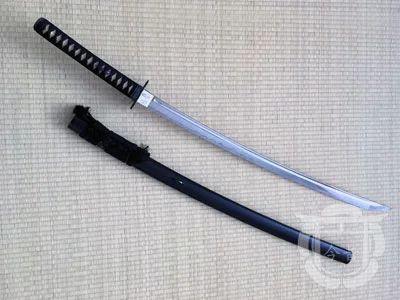
Après la trempe, le forgeron cède la place à un autre artisan : le polisseur, ou togishi.
Son travail de plusieurs jours, voire plusieurs semaines, consistera à faire ressortir la beauté de la lame tout en lui donnant son tranchant final à l’aide de pierres à aiguiser de différentes natures.
Le polissage s’effectue en deux étapes distinctes.
La première, le ji-togi, permet au polisseur de nettoyer la lame pour lui donner un bel aspect exempt d’impuretés liées à l’oxydation.
On passe ensuite au shiage qui consistera à mettre en valeur l’esthétique de la forge.
Pour finir, la lame sera soit montée sur un support sobre en bois clair, ce qu’on appelle un shirasaya, ou sous forme de sabre complet dont chaque élément (katana et fourreau) aura aussi été réalisé avec un grand soin.
La tsuka (poignée) et le saya (fourreau) sont réalisés sur mesure pour s’ajuster parfaitement à la lame par un artisan dont c’est la spécialité.
Un autre encore se chargera du tsukamaki, l’art de poser le « cordage » de la poignée sur la peau de raie ou de requin. Cette tresse en soie donne cet aspect caractéristique aux manches des katanas.
Une fois finalisé, le sabre sera plus qu’une arme. Il deviendra une véritable œuvre d’art exposé sur un support horizontal en bois laqué. Il est assez courant que ce type d’arme soit légué au sein d’une même famille, de génération en génération.
La fabrication d’un katana traditionnel japonais n’a maintenant plus de secret pour vous. Notez cependant que contrairement aux couteaux, dagues, poignards et autres armes à deux mains ou non, le shinken, katana utilisé dans la pratique des arts martiaux japonais, est très tranchant, ce qui en fait une arme blanche redoutable à laquelle il faudra faire attention. Si vous êtes envouté par la beauté du vrai katana japonais, sachez que nous pouvons passer commande auprès de maîtres artisans renommés.
L'artisan qu'on voit travailler n'est autre que Fujiwara Kanefusa 26ème du nom, un des forgerons les plus connus de la région de Seki, ville célèbre pour ses forges depuis près de 700 ans.
De la préparation du tamahagane jusqu'au montage final, la réalisation de ce sabre aura duré 10 mois.